Alcast Company Can Be Fun For Everyone
Alcast Company Can Be Fun For Everyone
Blog Article
The Single Strategy To Use For Alcast Company
Table of ContentsWhat Does Alcast Company Mean?Alcast Company for DummiesUnknown Facts About Alcast CompanyAlcast Company Fundamentals ExplainedSee This Report on Alcast CompanyThe Ultimate Guide To Alcast Company
The subtle distinction hinges on the chemical material. Chemical Contrast of Cast Aluminum Alloys Silicon advertises castability by reducing the alloy's melting temperature and improving fluidness during spreading. It plays a crucial function in permitting intricate mold and mildews to be loaded accurately. Furthermore, silicon adds to the alloy's stamina and wear resistance, making it valuable in applications where durability is critical, such as automotive parts and engine components.It additionally improves the machinability of the alloy, making it easier to process into finished products. In this way, iron adds to the general workability of aluminum alloys.
Manganese adds to the stamina of light weight aluminum alloys and improves workability (aluminum metal casting). It is typically made use of in wrought aluminum items like sheets, extrusions, and profiles. The visibility of manganese help in the alloy's formability and resistance to breaking during fabrication processes. Magnesium is a light-weight component that gives toughness and influence resistance to light weight aluminum alloys.
How Alcast Company can Save You Time, Stress, and Money.
It permits the manufacturing of lightweight elements with outstanding mechanical properties. Zinc improves the castability of light weight aluminum alloys and aids manage the solidification procedure throughout spreading. It improves the alloy's stamina and solidity. It is frequently discovered in applications where detailed forms and fine information are needed, such as ornamental castings and particular automotive components.
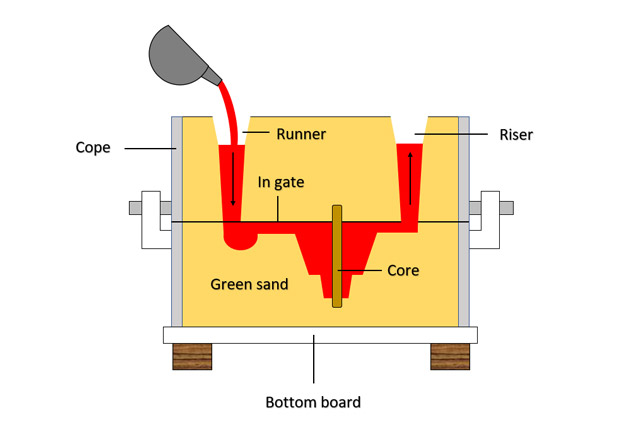
The main thermal conductivity, tensile strength, yield strength, and prolongation vary. Select appropriate resources according to the performance of the target product produced. Amongst the above alloys, A356 has the greatest thermal conductivity, and A380 and ADC12 have the most affordable. The tensile limit is the opposite. A360 has the most effective yield strength and the highest possible elongation price.
Alcast Company Things To Know Before You Buy
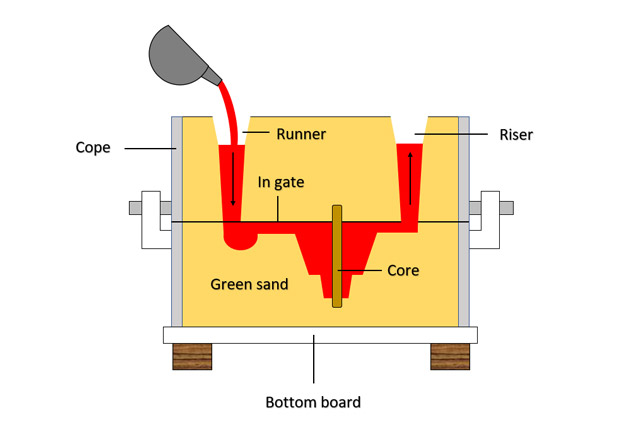
In precision casting, 6063 is appropriate for applications where elaborate geometries and premium surface coatings are extremely important. Examples include telecommunication units, where the alloy's remarkable formability permits sleek and visually pleasing designs while keeping structural stability. Similarly, in the Lights Solutions sector, precision-cast 6063 parts develop sophisticated and reliable lights components that call for detailed forms and great thermal performance.
It brings about a better surface coating and much better corrosion resistance in A360. The A360 shows exceptional elongation, making it optimal for complex and thin-walled parts. In accuracy casting applications, A360 is fit for sectors such as Customer Electronic Devices, Telecommunication, and Power Tools. Its boosted fluidity allows for complex, high-precision elements like mobile phone coverings and interaction tool housings.
The Greatest Guide To Alcast Company
Its one-of-a-kind residential or commercial properties make A360 a valuable choice for precision casting in these industries, enhancing item toughness and quality. Aluminum alloy 380, or A380, is an extensively used casting alloy with numerous distinct features. It provides exceptional castability, making it an optimal option for accuracy casting. A380 exhibits great fluidness when molten, ensuring intricate and in-depth molds are accurately duplicated.
In precision spreading, aluminum 413 beams in the Customer Electronic Devices and Power Equipment industries. This alloy's superior deterioration resistance makes it an exceptional choice for outdoor applications, making certain lasting, durable products in the mentioned markets.
Some Known Incorrect Statements About Alcast Company
Once you have determined that the light weight aluminum die casting procedure is suitable for your job, a vital next action is selecting one of the most appropriate alloy. The light weight aluminum alloy you select will substantially impact both the casting process and the buildings of the final item. Due to this, you must make your choice very carefully and take an enlightened method.
Figuring out the most ideal aluminum alloy for your application will mean evaluating a wide selection of characteristics. The first category addresses alloy attributes that affect the production process.
Getting The Alcast Company To Work
The alloy you choose for die casting straight influences a number of facets of the casting process, like exactly how simple the alloy is to collaborate with and if it is susceptible to casting problems. Warm splitting, also called solidification fracturing, is a regular die casting flaw for light weight aluminum alloys that can result in inner or surface-level tears or cracks.
Particular light weight aluminum alloys are much more vulnerable to warm fracturing than others, and your selection must consider this. An additional usual flaw located in the die spreading of aluminum is die soldering, which is when the cast sticks to the die wall surfaces and makes ejection tough. It can damage both the cast and the die, so you should try to find alloys with high anti-soldering residential properties.
Deterioration resistance, which is already a significant feature of aluminum, can vary significantly from alloy to alloy and is an important characteristic to consider relying on the environmental conditions your item will be subjected to (aluminum foundry). Use resistance is another residential property frequently looked for in aluminum products and can separate some alloys
Report this page